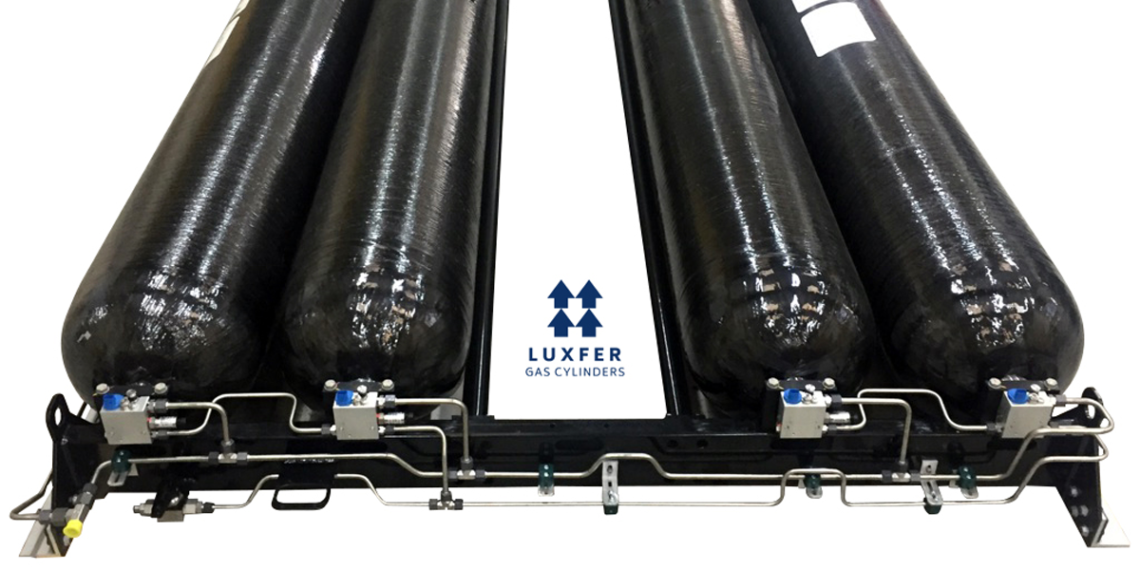
Luxfer : l’hydrogène au service du transport de demain
L’entreprise Luxfer fabrique des réservoirs permettant de stocker l’hydrogène des véhicules. Didier Richard, en charge du développement de l’entreprise, explique pourquoi l’hydrogène est aujourd’hui une énergie sécurisée.
En quoi votre système de « Vanne-réservoir-système sécurité autour du réservoir » est-il un organe essentiel de la mobilité hydrogène ?
Didier Richard : Aujourd’hui pour pouvoir assurer cette mobilité, vous avez besoin de stocker l’hydrogène. Chez Luxfer, nous fabriquons des bouteilles qui permettent de stocker l’hydrogène à 350 bars et qui ont des volumes allant de 28 à 322 litres. Comme la première valeur de notre entreprise est la sécurité, nous avons un degré d’exigence très élevé. On entend encore trop souvent parler d’hydrogène comme de véritables « bombes » que l’on mettrait sur le toit des bus, mais il faut démystifier le danger de l’hydrogène. Effectivement, il s’agit d’un gaz inflammable, et c’est justement pourquoi la fabrication des réservoirs est très contrôlée et normée ! Nous fabriquons des bouteilles pour gaz haute pression depuis la fin de la Seconde guerre mondiale, et nous n’avons jamais eu de soucis de cet ordre.
Pouvez-vous nous expliquer leur fabrication ?
D. R. : Pour fabriquer une bouteille, nous partons d’un tube en aluminium que l’on calibre et sur lequel nous réalisons de nombreux tests et traitements, puis nous procédons à l’enrobage filamentaire. On enrobe une fibre de carbone sur la totalité de la bouteille en aluminium qui procure 90% de la résistance du réservoir. Une fois les bouteilles terminées, nous procédons à une très large batterie de tests, dont des cyclages, c’est-à-dire remplir et vider de gaz ces bouteilles des milliers de fois. Nous réalisons aussi des tests d’éclatement qui nous permettent d’affirmer que même à des niveaux de pression beaucoup plus élevés que la pression de service, nos bouteilles n’éclatent pas. Enfin, réalisons des tests de tenue au feu et nous tirons à balles réelles sur nos réservoirs pour s’assurer de leur très grande solidité. Mais même si nous avons développé une grande prévention, nous avons aussi des garanties concernant le comportement de nos bouteilles en cas d’accident. Il y a quelques années, à Los Angeles, il y avait des travaux sur la voirie et le tracé des bus avait été changé, mais un conducteur s’est trompé d’itinéraire. Il est passé sous un pont, sans s’apercevoir qu’il manquait quelques centimètres. En passant, nos bouteilles se sont écrasées, et un système de surpression s’est mis en marche, dégageant le gaz qui était dans les bouteilles. Elles ont été détériorées mais à aucun moment il n’y a eu de risque d’explosion.
Cette sécurité du réservoir nécessite un savoir-faire de pointe. Comment gérez-vous cela, humainement parlant ?
D. R. : Nous avons une équipe d’ingénieurs qui travaillent sur ces projets, et qui sont spécialisés dans tout ce qui concernant les équipements à pression et les matériaux composites. Nous avons des employés très compétents ! Le savoir-faire dans ces domaines de technologies de pointe est une part importante de la qualité de nos fabrications. Ce savoir-faire nous permet de proposer en permanence des innovations en faveur de la sécurité et de la capacité de stockage pour nos clients fabricants de bus. C’est ainsi que récemment nous sommes parvenus à produire des bouteilles en composite aluminium et carbone pour le gaz naturel plus légères que les bouteilles composite plastique et carbone. C’est une prouesse technologique à mettre au crédit de toute l’équipe de Luxfer !
Didier Richard est en charge du développement EMEA de Luxfer Gas Cylinders