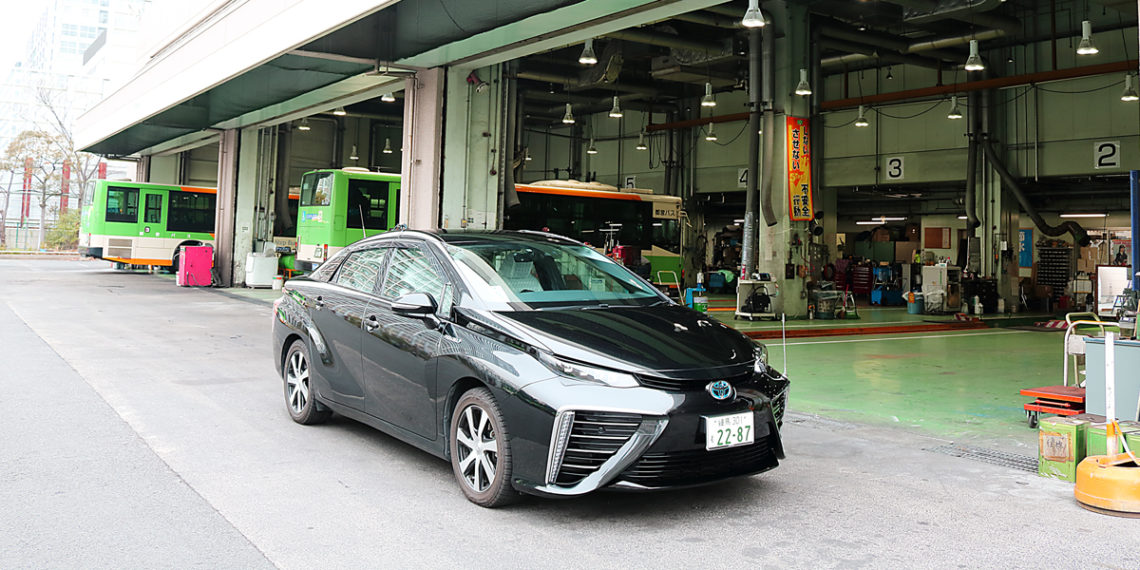
Miraï : un processus de fabrication tourné vers l’avenir
Rendez-vous au siège social de Toyota, 1 rue Toyota, dans la ville de Toyota, pour découvrir l’usine Miraï (« futur » en français). Immersion avec les équipes.
Le chariot-élévateur
Aujourd’hui, près de cent quatre-vingts chariots-élévateurs à motorisations thermiques et électriques roulent au siège social de Toyota, ce qui peut paraître paradoxal dans un lieu où sont fabriqués des véhicules 100 % hydrogène, mais la situation est en train de changer.
Depuis fin janvier 2017, deux de ces chariots-élévateurs circulent grâce à une pile à combustible. Le stock d’hydrogène qui leur est réservé étant encore insuffisant, ils ne peuvent pas rouler plus de 55 % du temps de travail de sept heures et cinquante minutes par jour. Or, là encore, Toyota innove et construit actuellement une station de recharge sur-mesure pour minimiser cette perte de temps et surtout limiter les émissions de GES.
Le véhicule Miraï en bref
Si les véhicules électriques ont chacun leur prise selon le constructeur acheté, tous les véhicules à hydrogène disposent d’un modèle standard, quelle que soit la marque. Un véhicule à hydrogène roule en effet avec de l’électricité produite dans son moteur et rejette de l’eau et de la vapeur. Cette eau pure peut également être stockée dans un réservoir qui peut accueillir quarante litres.
La MiraÏ, qui produit donc sa propre électricité, possède même, au milieu des sièges arrière, une prise électrique de 1 500 Watts où les passagers peuvent brancher leur téléphone portable ou leur ordinateur. Une famille de quatre personnes peut aussi s’en servir comme transformateur pendant une semaine en cas de coupure d’électricité ou dans un endroit sans réseau électrique comme la montagne.
L’assemblage
Il se fait en treize étapes, chacune confiée à un technicien ultra-qualifié. Dix hommes et trois femmes, dont la plus jeune commence sa deuxième année professionnelle, respectent un processus de stop-and-go : soixante-douze minutes entre leurs mains, puis le véhicule passe à l’action suivante.
D’abord, la carrosserie est posée : le fuselage, le capot et le coffre, puis c’est au tour de la motorisation : moteur, pile à combustible, les deux réservoirs et la batterie électrique, auxquels s’ajoutent les pneus. Enfin, tout l’intérieur est comblé : vitres, sièges et tapis de sols. Ultime étape :
la pose des portes qui ferment la voiture, au sens propre comme au sens figuré.
La formation des techniciens
Longtemps, cette usine a été l’atelier des véhicules haut de gamme utilisés pour les courses automobiles et fabriqués de manière artisanale. Comme ces stars de la route, les Miraï sont conçues en petites quantités car la qualité de la sécurité est primordiale. Manuels et intellectuels, les ouvriers acquièrent tant d’informations sur chaque étape qu’ils peuvent améliorer voire innover leur maîtrise d’ouvrage en l’espace de quelques semaines. Ils peuvent en outre réparer voire remplacer une machine sur une autre chaîne d’assemblage. Il arrive même parfois qu’ils soient envoyés dans les autres usines du groupe pour aider ! L’un raconte, en souriant, avoir déjà remarqué des nuances de peinture de la même couleur mais de lots différents. Un autre s’amuse, lui, à entretenir des vieux véhicules de collection sur son temps libre.